Alliance Calibration, a Transcat Company
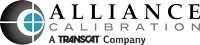
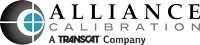
Alliance Calibration, a Transcat Company, was founded in 1999 and headquartered in Cincinnati, OH. Serving the central region of the United States, Alliance specialized in delivering quality calibration services to the automotive, defense, government, aeronautical, medical, pharmaceutical, and power generation markets.
After its acquisition in June 2022, Alliance Calibration joined the leading nationwide calibration services team at Transcat as its Cincinnati Calibration Lab. The following services that you relied upon Alliance Calibration to provide are now available to you through Transcat.
Accredited Calibration Services – Now Transcat’s Cincinnati Calibration Lab


Electrical Calibration Services
- Multimeters
- Oscilloscopes
- Power Supplies
- Decade Resistors
- Voltage Probes
- DLROs
- Dielectric Test Sets
- HiPot Testers
- Clamp Meters
- Insulation Testers
- and more
Dimensional Calibration Services
- Cylinder Plugs
- Gage Blocks
- Hardness Testers
- Height Gages
- Height Masters
- Indicators
- Length Standards
- Micrometers
- Depth Gages
- Calipers
- Plain Rings
- Radius Gages
- Surface Plates
- Thread Rings
- Thread Plugs
- Pin Gages
- Surface Profilometers
- and more
Meter Calibration Services
- Accelerometers
- Air Data Multimeters
- Ammeters
- Balometers
- Clamp Meters
- DLROs
- Durometers
- Hydronic Manometers
- Multimeters
- Manometers
- Panel Meters
- Profilometers
- Tachometers
- Thermometers
- and more
Torque Calibration Services
- Torque Screwdrivers
- Torque Wrenches
- Torque Multipliers
- Torque Transducers
- Torque Watches
- and more
Force Calibration Services
- Force gage calibration up to
2,000 lbf tension and compression
Load Cell Calibration Services
- Load cell calibration from 6 to
20,000 lbf compression
Alliance Calibration customers can access their calibration records through the IndySoft Portal.